Since the vast majority of our customers are taller than 6’4″ and well over 200 pounds, we at Zinn Cycles build wheels for big riders every day, be they 700C road, gravel, and cyclocross wheels, 29er (including 29+) mountain bike wheels, 750D wheels, 32 inch wheels, and even 36 inch wheels. The quality of the build is critical, and the rim, hubs, spokes (and spoke count) must be chosen appropriately for the rider.
Here is a list of our main criteria for building a set of strong bicycle wheels.
- High spoke counts
- Double-butted spokes
- Spoke-bracing angle
- Rim stiffness
- Rim strength
- Threadlocked nipples
- Spoke holes further from the edge of the hub flange
- Robust freehub
- Through axles
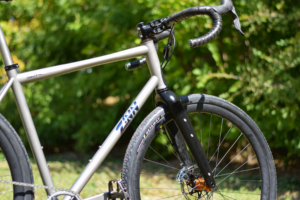
Selecting the components
Rims
Starting from the outside and working inward, the importance of stiff, strong rims cannot be understated for big riders. The rims work together with the spokes in the dynamic structure that is a wheel, and, the stiffer the rim, and the higher its spoke count, the less the spokes vary in tension as a wheel rolls along. A taller cross section makes a rim stiffer, and greater wall thickness, coupled with a good choice of alloy, make it stronger. For instance, the Velocity Chukker rim has a deep, V-shaped cross section combined with a thick wall and a strong alloy, and for this reason, it is often our choice for a road wheel for a big rider. Click here to Order Wheels Online.
Strong Bicycle Hubs
The hub must be strong, have stiff hub shells, strong flanges, a robust freehub, drilled for high spoke count, a wide spoke bracing angle, and a through axle. Big guys pedaling hard in low gear can twist the rear hub shell, as can disc brakes applied hard under heavy load and high speed, so a stiff hub shell is a no-brainer. Hub strength
Through-axle hubs strengthen both the wheel and the frame and fork and are a must for heavy riders. Through-axle dropouts are simply holes, rather than slots, with a threaded nut integrated into them, be they for 12mm, 15mm, or 20mm up front and 12mm in the rear. If you have quick-release dropouts, you can still use a 10mm through axle in the rear and a 9mm in the front with a nut on the end, instead of a hollow axle with a skinny quick-release skewer inside. The 9mm or 10mm through axle fills the entire space of the dropout providing much better dropout support. Both ends of the bike will track better by virtue of the stiff axles tying the fork legs and rear end together, particularly on full suspension bikes, making the outer fork legs slide smoothly over the inner legs and the rear swingarm members to track without wobble. Also, the rear through-axle will prevent the hogging out of the right rear dropout that can happen, particularly on mountain bikes, with a big, strong rider putting out high torque in low gear. This may have happened to your dropout if you cannot keep your rear wheel from pulling over to the left chainstay, no matter how tight you keep your quick-release skewer. click here to order hubs online
Secondly, I would recommend high spoke counts (we generally use 32 or 36 spokes), with high-quality, double-butted 2.0/1.8mm (14/15-gauge) stainless steel spokes with (brass) thread-locked nipples to prevent them from loosening up (we use DT Competition spokes with DT Pro Lock nipples or Sapim SecureLoc). Contrary to what you might think, the lighter, stretchier, double-butted spokes make for a longer-lasting wheel than would heavier, straight-gauge 2.0mm (14-gauge) spokes of the same quality. As the spokes stretch, they move some stress concentration from the weakest points at the elbow and nipple, and the nipples stay in contact with the rim under high wheel deformations (often occurring under somebody big), reducing rim fatigue. Click Here to order custom built wheels online.
An obvious wear factor on a wheel is impact — a guy who unweights the bike for train tracks or potholes will have less impact damage than the guy who bangs into everything fully weighted on the saddle. And, of course, the greater the weight (force) on the wheel on impact, the greater the damage it will sustain.
But often, more important than impacts for wheel durability, is fatigue, and that is dependent on weight and also on smoothness of the pedal stroke. At least half of the customers buying bikes or cranks from Zinn Cycles and Clydesdale Bicycles are over 250 pounds, and the ones with a hitch in their pedal stroke crack rear rims on factory-built wheels at every drive-side spoke nipple in short order. We have some 300-pound customers who get quite decent wheel wear, and others who break everything in no time; they break hub flanges and spokes, crack rims, and pull apart two-piece press-fit hubs.
The spokes loosen up because, as the wheel rolls, the section at the bottom becomes flattened (D-shaped). If you’re heavy enough, that flat spot is deep enough that it totally de-tensions the spoke that is at the bottom, since the nipple has lost contact with the rim. This allows each spoke to jiggle during that moment it’s at the bottom without tension and, over time, consequently unscrew.
Furthermore, as the wheel continues rolling, the flattened section of rim snaps back to its original shape, abruptly bringing that spoke that had been at the bottom back to full tension. If the spoke had been completely de-tensioned, the bang-bang-bang of the impact of the rim snapping back against the nipple with every single wheel rotation will fatigue not only the spoke, but also the rim at that spoke nipple. This will cause the rim to crack over time at each spoke nipple.
Rim cracking at each nipple is a bigger issue with aluminum spokes, because aluminum has less elasticity; an aluminum spoke is not stretched as much as a thin, steel spoke would be, so its nipple loses contact with the rim with less deformation of the rim when it is at the bottom. Thus, it requires less load on the wheel for that bang-bang-bang fatigue process to crack the rim if it’s built with aluminum spokes than if it’s built with steel spokes.
This is also why a double-butted steel spoke will result in longer life of both the rim and the spoke than will a straight-gauge steel spoke — because its thinner center section will stretch more at the same overall spoke tension. This keeps the nipple in contact with the rim better as it rolls, and its thicker ends will still protect it where the stress is most concentrated.
Until recently we avoided building carbon fiber wheels for riders over 250lbs due to the unavailability of higher spoke count carbon rims. We have now developed a line of carbon wheelsets built for big and heavy riders with some customized carbon rims with heavier duty material layups and higher spoke counts. Carbon does not fatigue like aluminum and is very light and stiff, so with the properly built carbon fiber rim, you can build a very strong wheel. Carbon fiber is more susceptible to impacts so it is very important to keep your tire pressure appropriate for your weight by checking it before every ride. This should help to avoid damage from impacts.